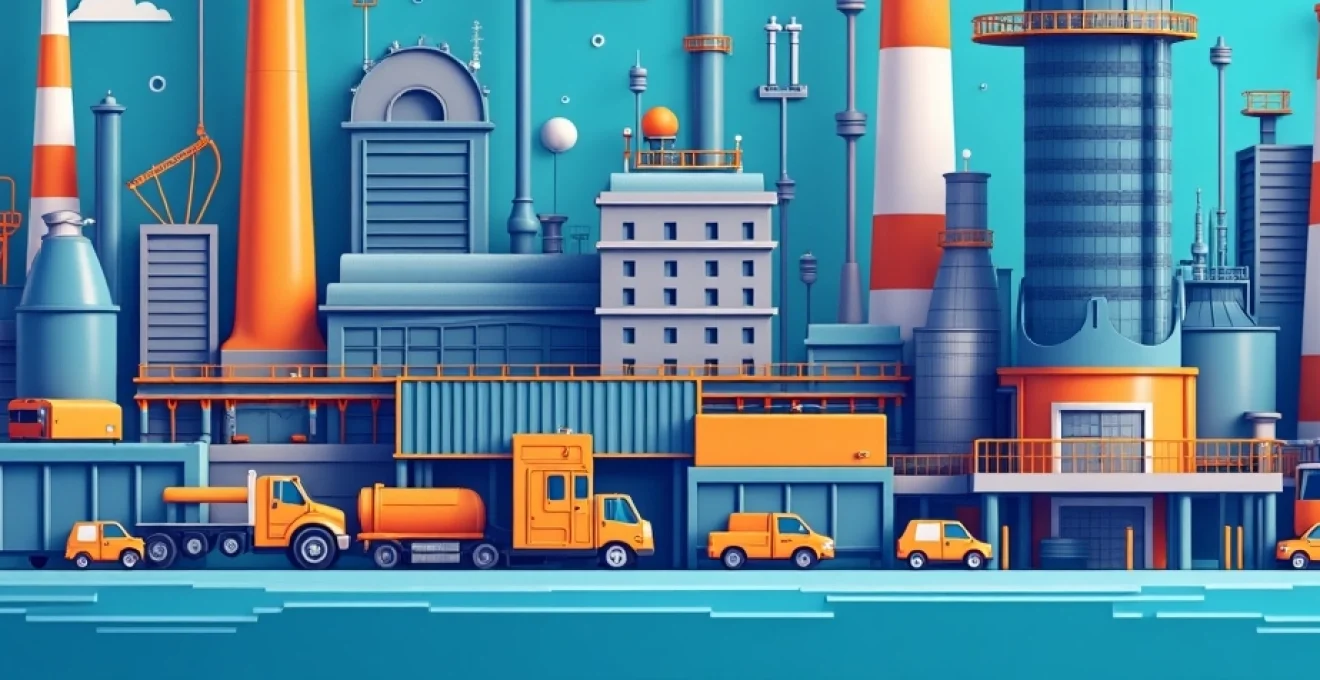
Les installations de production constituent le cœur battant de l'industrie moderne. Elles représentent l'ensemble des équipements, machines et systèmes interconnectés qui permettent la transformation des matières premières en produits finis. Dans un contexte de compétitivité accrue et d'évolution technologique rapide, la conception et l'optimisation de ces installations sont devenues des enjeux majeurs pour les entreprises manufacturières. De la flexibilité des lignes de production à l'intégration de technologies avancées, les installations modernes doivent relever de nombreux défis pour rester performantes et adaptées aux exigences du marché.
Types d'installations de production industrielle
Les installations de production industrielle se déclinent en plusieurs catégories, chacune adaptée à des besoins spécifiques de fabrication. On distingue notamment :
- Les lignes de production en série : conçues pour la fabrication de grandes quantités de produits identiques ou similaires
- Les ateliers de production par lots : flexibles et adaptés à la production de séries limitées
- Les unités de production continue : utilisées dans les industries de process comme la chimie ou l'agroalimentaire
- Les cellules de fabrication flexibles : combinant automatisation et adaptabilité pour des productions variées
Le choix du type d'installation dépend de nombreux facteurs tels que la nature des produits, les volumes de production visés, et la variabilité de la demande. Par exemple, l'industrie automobile privilégie souvent les lignes de production en série hautement automatisées, tandis que l'industrie aérospatiale opte plutôt pour des ateliers flexibles capables de s'adapter à des commandes spécifiques.
La tendance actuelle est à la flexibilité accrue des installations, permettant de basculer rapidement d'un type de production à un autre. Cette agilité est devenue un atout concurrentiel majeur dans un marché où la personnalisation des produits et la réactivité à la demande sont de plus en plus valorisées.
Conception et planification des systèmes de production
La conception d'une installation de production efficace nécessite une approche méthodique et multidisciplinaire. Elle débute par une analyse approfondie des besoins de production, des contraintes techniques et économiques, ainsi que des perspectives d'évolution à moyen et long terme. Cette phase initiale est cruciale pour définir les orientations stratégiques qui guideront l'ensemble du projet.
Analyse des flux de production avec la méthode VSM
La méthode Value Stream Mapping (VSM) est un outil puissant pour optimiser les flux de production. Elle consiste à cartographier l'ensemble des étapes de création de valeur, depuis la réception des matières premières jusqu'à la livraison du produit fini. Cette analyse permet d'identifier les goulots d'étranglement, les temps d'attente excessifs et les activités sans valeur ajoutée.
Grâce à la VSM, les concepteurs peuvent visualiser clairement le processus de production et proposer des améliorations ciblées. Par exemple, la réorganisation des postes de travail pour réduire les déplacements inutiles ou l'introduction de systèmes de gestion visuelle pour fluidifier les flux d'information.
Dimensionnement des lignes avec la simulation numérique
La simulation numérique est devenue un outil incontournable pour le dimensionnement des lignes de production. Elle permet de tester virtuellement différentes configurations et scénarios de production avant même la mise en place physique des équipements. Les logiciels de simulation offrent la possibilité de modéliser l'ensemble de l'installation, d'évaluer ses performances et d'identifier les points d'amélioration potentiels.
L'utilisation de jumeaux numériques pousse cette approche encore plus loin, en créant une réplique virtuelle exacte de l'installation qui peut être mise à jour en temps réel. Cette technologie facilite non seulement la conception initiale, mais aussi l'optimisation continue des processus de production.
Intégration de l'ergonomie dans la conception des postes
L'ergonomie des postes de travail est un aspect fondamental de la conception des installations modernes. Elle vise à adapter le travail à l'homme, et non l'inverse, pour améliorer à la fois la productivité et le bien-être des opérateurs. L'intégration de principes ergonomiques dès la phase de conception permet de réduire les risques de troubles musculo-squelettiques et d'améliorer la qualité du travail.
Les concepteurs utilisent des outils tels que la simulation 3D et la réalité virtuelle pour évaluer l'ergonomie des postes avant leur mise en place. Ces technologies permettent de tester différentes configurations et d'optimiser les mouvements des opérateurs, réduisant ainsi la fatigue et les risques d'accidents.
Optimisation du layout avec la méthode SLP
La méthode Systematic Layout Planning (SLP) est une approche structurée pour optimiser l'agencement spatial des installations de production. Elle se base sur l'analyse des relations entre les différentes activités et équipements pour proposer un layout optimal. L'objectif est de minimiser les déplacements, optimiser l'utilisation de l'espace et faciliter les flux de matériaux et d'informations.
La méthode SLP comprend plusieurs étapes, notamment :
- L'analyse des relations entre les activités
- L'établissement d'un diagramme relationnel
- La détermination des besoins en espace
- L'élaboration de plusieurs alternatives de layout
- L'évaluation et la sélection du meilleur agencement
Cette approche méthodique permet d'aboutir à des configurations d'ateliers plus efficientes, réduisant les temps de cycle et améliorant la productivité globale de l'installation.
Technologies clés des installations modernes
Les installations de production modernes intègrent un large éventail de technologies avancées visant à améliorer la flexibilité, la productivité et la qualité. Ces innovations transforment profondément le paysage industriel, ouvrant la voie à des usines plus intelligentes et plus réactives.
Systèmes de production flexibles (FMS)
Les Systèmes de Production Flexibles (FMS) représentent une évolution majeure dans la conception des installations industrielles. Ces systèmes combinent des machines-outils à commande numérique, des robots et des systèmes de manutention automatisés, le tout piloté par un système informatique centralisé. La flexibilité du FMS réside dans sa capacité à produire une variété de pièces ou de produits avec un minimum de temps de changement entre les productions.
Les avantages des FMS incluent :
- Une réduction significative des temps de configuration
- Une meilleure utilisation des équipements
- Une augmentation de la productivité globale
- Une plus grande réactivité aux changements de la demande
Ces systèmes sont particulièrement adaptés aux industries confrontées à une forte variabilité des produits et des volumes de production, comme l'aérospatiale ou l'automobile haut de gamme.
Cobotique et robotique collaborative
La cobotique , ou robotique collaborative, représente une nouvelle approche de l'automatisation industrielle. Contrairement aux robots traditionnels isolés dans des cages de sécurité, les cobots sont conçus pour travailler aux côtés des opérateurs humains. Ils combinent la précision et l'endurance des machines avec la flexibilité et l'intelligence des humains.
Les cobots offrent plusieurs avantages :
- Une meilleure ergonomie en assistant les opérateurs dans les tâches pénibles
- Une flexibilité accrue grâce à leur facilité de programmation et de redéploiement
- Une optimisation de l'espace de production, les cobots ne nécessitant pas de barrières de sécurité imposantes
- Une amélioration de la qualité et de la régularité des opérations
L'intégration des cobots dans les installations de production permet d'atteindre un équilibre optimal entre automatisation et intervention humaine, ouvrant la voie à des processus de fabrication plus agiles et plus efficaces.
Internet industriel des objets (IIoT)
L'Internet Industriel des Objets (IIoT) constitue l'un des piliers de l'Industrie 4.0. Il s'agit de l'application des technologies de l'Internet des Objets au domaine industriel, permettant une connectivité et une intelligence accrues des équipements de production. Les capteurs, les actionneurs et les dispositifs de communication intégrés aux machines génèrent un flux continu de données qui peuvent être analysées pour optimiser les processus de production.
Les applications de l'IIoT dans les installations de production sont nombreuses :
- Maintenance prédictive basée sur l'analyse en temps réel de l'état des équipements
- Optimisation de la consommation énergétique
- Traçabilité améliorée des produits tout au long de la chaîne de production
- Ajustement automatique des paramètres de production en fonction des variations de qualité
L'IIoT ouvre la voie à des installations de production plus intelligentes, capables de s'auto-optimiser et de réagir en temps réel aux changements de conditions de production.
Fabrication additive et impression 3D industrielle
La fabrication additive, communément appelée impression 3D, révolutionne la manière dont certains composants sont produits dans l'industrie. Cette technologie permet de créer des pièces complexes en déposant des couches successives de matériau, offrant une liberté de conception sans précédent.
Dans les installations de production modernes, la fabrication additive trouve sa place dans plusieurs domaines :
- Prototypage rapide pour accélérer le développement de nouveaux produits
- Production de pièces de rechange à la demande, réduisant les besoins en stockage
- Fabrication de composants personnalisés pour des productions en petites séries
- Création d'outillages et de gabarits sur mesure pour optimiser les lignes de production
L'intégration de l'impression 3D dans les installations de production traditionnelles crée des synergies intéressantes, combinant la flexibilité de la fabrication additive avec l'efficacité de la production de masse.
Gestion et pilotage de la production
La gestion efficace des installations de production repose sur des systèmes de pilotage avancés qui permettent de superviser, contrôler et optimiser l'ensemble des processus de fabrication. Ces outils jouent un rôle crucial dans la performance globale de l'usine.
MES (manufacturing execution system) et traçabilité
Le Manufacturing Execution System (MES) est un système informatique qui assure le lien entre la planification de la production (ERP) et le contrôle des équipements sur le terrain. Il joue un rôle central dans la gestion opérationnelle de la production en temps réel. Les fonctionnalités d'un MES incluent :
- L'ordonnancement détaillé de la production
- Le suivi de l'avancement des ordres de fabrication
- La gestion de la qualité et de la maintenance
- La collecte et l'analyse des données de production
Un aspect crucial du MES est sa capacité à assurer une traçabilité complète des produits tout au long du processus de fabrication. Cette traçabilité est essentielle pour garantir la qualité, faciliter les rappels de produits si nécessaire, et répondre aux exigences réglementaires dans certains secteurs comme l'agroalimentaire ou la pharmacie.
Lean manufacturing et amélioration continue
Le lean manufacturing est une approche de gestion visant à éliminer les gaspillages et à optimiser la création de valeur dans les processus de production. Cette philosophie, initialement développée par Toyota, s'est largement répandue dans l'industrie mondiale. Elle repose sur plusieurs principes clés :
- L'élimination des activités sans valeur ajoutée
- La production en flux tiré pour répondre précisément à la demande
- La recherche de la qualité parfaite dès la première fois
- L'implication et la responsabilisation des employés
L'amélioration continue, ou Kaizen en japonais, est un pilier du lean manufacturing. Elle encourage les petites améliorations incrémentales régulières plutôt que les grands changements ponctuels. Cette approche favorise l'innovation au quotidien et l'adaptation constante des installations de production aux évolutions du marché et des technologies.
Maintenance prédictive et GMAO
La maintenance prédictive représente une évolution majeure dans la gestion des équipements industriels. Contrairement à la maintenance préventive basée sur des intervalles fixes, la maintenance prédictive utilise des données en temps réel pour anticiper les pannes avant qu'elles ne se produisent. Cette approche repose sur :
- L'utilisation de capteurs pour surveiller en continu l'état des équipements
- L'analyse avancée des données pour détecter les signes précurseurs de défaillance
- Des algorithmes d'intelligence artificielle pour prédire les besoins de maintenance
La Gestion de Maintenance Assistée par Ordinateur (GMAO) est un outil essentiel pour mettre en œuvre une stratégie de maintenance efficace. Elle permet de planifier, suivre et optimiser toutes les activités de maintenance, qu'elles soient correctives, préventives ou prédictives. L'intégration de la GMAO avec les systèmes de production et d'analyse de données ouvre la voie à une maintenance véritablement intelligente et proactive.
Sécurité et conformité des installations
La sécurité des installations de production est une priorité absolue pour toute entrepr
ise industrielle. Au-delà des considérations de productivité, la protection des travailleurs et la conformité aux réglementations sont des aspects fondamentaux de la conception et de l'exploitation des installations de production. Les enjeux de sécurité couvrent un large spectre, allant de la prévention des accidents du travail à la sécurité des procédés industriels.
Les principaux axes de la sécurité dans les installations de production comprennent :
- La sécurité des machines et des équipements
- L'ergonomie des postes de travail
- La gestion des risques chimiques et biologiques
- La prévention des incendies et des explosions
- La sûreté des systèmes de contrôle-commande
La mise en conformité des installations avec les normes et réglementations en vigueur est un processus continu qui nécessite une veille réglementaire active et des audits réguliers. Les certifications telles que l'ISO 45001 pour la santé et la sécurité au travail sont devenues des standards incontournables pour de nombreuses entreprises industrielles.
L'intégration des technologies de l'Industrie 4.0 soulève de nouveaux défis en matière de sécurité, notamment en ce qui concerne la cybersécurité des systèmes industriels connectés. La protection des données de production et la sécurisation des communications entre les différents équipements sont devenues des préoccupations majeures pour les industriels.
Tendances futures des installations de production
L'évolution rapide des technologies et des modèles économiques façonne les tendances futures des installations de production. Ces tendances visent à répondre aux défis de flexibilité, de durabilité et de personnalisation de masse auxquels l'industrie est confrontée.
Usines intelligentes et industrie 4.0
Le concept d'usine intelligente, ou smart factory, est au cœur de la vision de l'Industrie 4.0. Il s'agit d'installations de production hautement numérisées et interconnectées, capables de s'auto-optimiser et de s'adapter en temps réel aux variations de la demande et des conditions de production. Les caractéristiques clés des usines intelligentes incluent :
- L'intégration complète des systèmes d'information et de production
- L'utilisation massive de capteurs et d'objets connectés
- L'analyse en temps réel des données de production
- L'automatisation avancée et l'utilisation de robots collaboratifs
- La flexibilité et la reconfigurabilité des lignes de production
Ces usines du futur promettent des gains significatifs en termes de productivité, de qualité et de personnalisation des produits. Elles permettent également une meilleure utilisation des ressources et une réduction de l'impact environnemental de la production industrielle.
Jumeaux numériques et simulation en temps réel
Les jumeaux numériques représentent une avancée majeure dans la gestion des installations de production. Il s'agit de répliques virtuelles exactes des installations physiques, mises à jour en temps réel grâce aux données collectées par les capteurs sur le terrain. Ces modèles virtuels permettent :
- La simulation et l'optimisation des processus de production
- La prédiction des performances et la détection précoce des anomalies
- La formation des opérateurs dans un environnement virtuel sécurisé
- Le test de nouvelles configurations sans perturber la production réelle
L'utilisation des jumeaux numériques s'étend au-delà de la phase d'exploitation, couvrant l'ensemble du cycle de vie des installations, de la conception initiale jusqu'au démantèlement. Cette approche permet une optimisation continue et une adaptation agile des systèmes de production aux évolutions du marché.
Production décentralisée et micro-usines
La tendance à la décentralisation de la production se manifeste par l'émergence de micro-usines et de systèmes de production distribués. Ces installations de taille réduite, mais hautement flexibles, permettent de rapprocher la production des consommateurs finaux. Les avantages de cette approche incluent :
- Une réduction des coûts et de l'impact environnemental du transport
- Une meilleure adaptation aux marchés locaux
- Une plus grande résilience face aux perturbations de la chaîne d'approvisionnement
- La possibilité de personnaliser les produits à l'échelle locale
Les micro-usines s'appuient souvent sur des technologies avancées telles que l'impression 3D et les systèmes de production modulaires pour atteindre un niveau élevé de flexibilité. Cette approche ouvre la voie à de nouveaux modèles d'affaires, comme la production à la demande ou la fabrication en tant que service.
En conclusion, les installations de production du futur seront caractérisées par leur intelligence, leur flexibilité et leur capacité à s'adapter rapidement aux changements. L'intégration des technologies numériques, de l'intelligence artificielle et des nouvelles approches de production distribuée transformera profondément le paysage industriel, ouvrant de nouvelles opportunités pour l'innovation et la création de valeur.